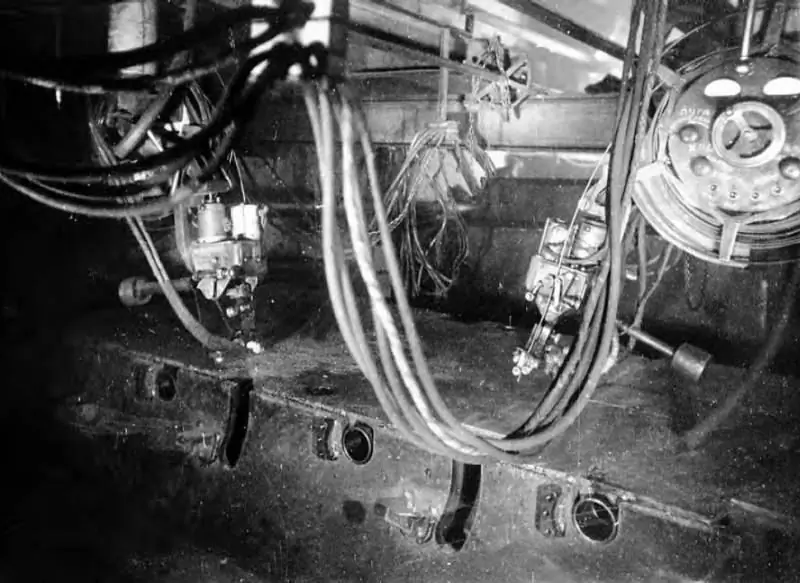
Укротяване на бронята
Един от основните проблеми при производството на корпуси и кули на средни танкове Т-34 е напукването на заварените части. Всичко е свързано с високата твърдост на бронята 8C, когато до заварения шев се образуват малки разкъсвания или микропукнатини. Наличието на остатъчни напрежения след заваряване за първи път след производството на бронирания автомобил не се усети, но с течение на времето излезе с пукнатини с дължина до 500 мм. Всичко това, разбира се, намали удароустойчивостта на бронята на танковете. За да се реши този проблем, веднага след организирането на производството на евакуираните предприятия, през втората половина на 1942 г., бяха привлечени специалисти от Бронирания институт (ЦНИИ-48) и Института по електрозаваряване на Академията на науките на СССР. Изследването е проведено в две предприятия: Уралския танков завод № 183 в Нижни Тагил и Уралския завод за тежко инженерство в Свердловск. Общо от юли до октомври металурзите и изследователите на материали изследват образуването на пукнатини по време на заваряването на около 9500 бронирани части. Целта на изследването беше да се намери най -оптималният химически състав на бронята 8С. Оказа се, че най -важният компонент в бронята в тази ситуация е въглеродът. Ако съдържанието му в бронята е повече от 0,25%, твърдостта на втвърдената зона в областта на заварения шев рязко се увеличава, което неизбежно води до напукване.
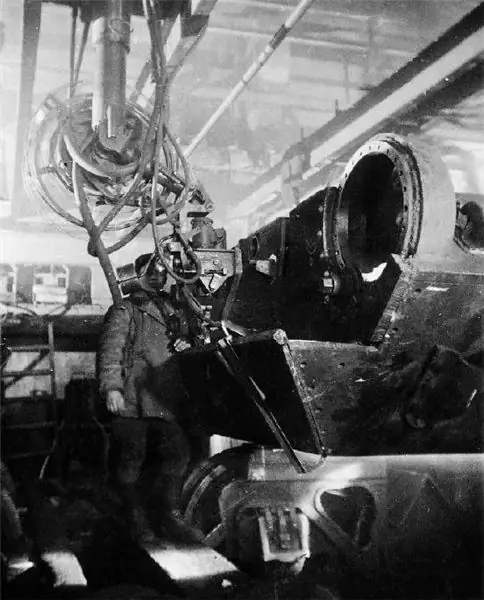
Но не беше лесно да се осигури такова ниско съдържание на въглерод в бронираната стомана в мирно време, а по време на война това изобщо изглеждаше невъзможно. Малки "козметични" промени в заваръчния цикъл чрез използването на аустенитни електроди, многоролкова система за нанасяне на заваръчни шевове и ниско темпериране на сглобките след заваряване направиха възможно повишаването на горната граница на съдържанието на въглерод само до 0,28%. Между другото, в германската танкова индустрия дори не са чували за такива сериозни изисквания към бронята на танковете - средно делът на въглерода е бил в диапазона от 0,4-0,5%. Решението на проблема с появата на пукнатини в зоната на заваряване е предварително загряване на частите до 150-200 градуса по Целзий, последвано от бавно охлаждане на частите след заваряване до 100 градуса за 30 минути. За тази цел Бронираният институт разработи специални индуктори, които осигуряват локално нагряване на бронирани части в зоната на газово рязане или заваряване. В Уралския завод за тежко машиностроене бяха използвани индуктори за заваряване на съединението на челната част със страните и покрива, както и при изрязване на балансиращите отвори в закалените странични части на резервоарите. По този начин проблемът с напукването при заваряване на средновъглеродни бронирани стомани беше решен. С течение на времето практиката на завода в Свердловск беше разширена и на други цистерни.
Заваръчни машини
През юли 1941 г. по заповед на Съвета на народните комисари Институтът по електрозаваряване на Академията на науките на СССР е евакуиран в Нижни Тагил. Ето защо за първи път в „Уралвагонзавод“беше въведено автоматично дъгово заваряване на резервоари. Разбира се, тази технология беше известна по-рано, но групата на академик Евгений Оскарович Патон със служители на ЦНИИ-48 успя да я адаптира за заваряване на бронирани стомани. Един от изключителните учени, допринесли за развитието на бронирано заваряване, беше Владимир Иванович Дятлов. Заедно със служителите на Харковския завод „Коминтерн“той реши проблема с напукването на бронята по време на заваряването, като въведе нисковъглеродна тел в заваръчната вана (повече за това по-долу). През 1942 г. учен, първият в света, открива явлението саморегулиране на дъговите процеси с консумиращ електрод, което дава възможност значително да се опрости проектирането на механизмите за подаване на заваръчни машини. Поради това беше възможно да се създадат сравнително прости заваръчни глави с един двигател, по-надеждни и по-евтини. Без Дятлов не би било възможно да се създадат ефективни потоци на базата на шлаки от доменни пещи на дървени въглища на Ашинския металургичен завод, които бяха наречени "шлакови потоци ША". От октомври 1943 г. ученият оглавява лабораторията на заваръчния Уралвагонзавод и остава на тази позиция до 1944 г., докато не бъде преместен в Централния изследователски институт по корабостроителни технологии.
Но да се върнем към легендарния Т-34, който никога не би се превърнал в толкова масивен танк, ако не беше автоматичното заваряване на бронираните му корпуси (кули) във фабрики No 183 и UZTM. Използването на автоматични заваръчни машини направи възможно намаляването на времето за заваряване с 3-6,5 пъти. В същото време са използвани поне 40 линейни метра заваръчни шевове за всеки танков корпус.
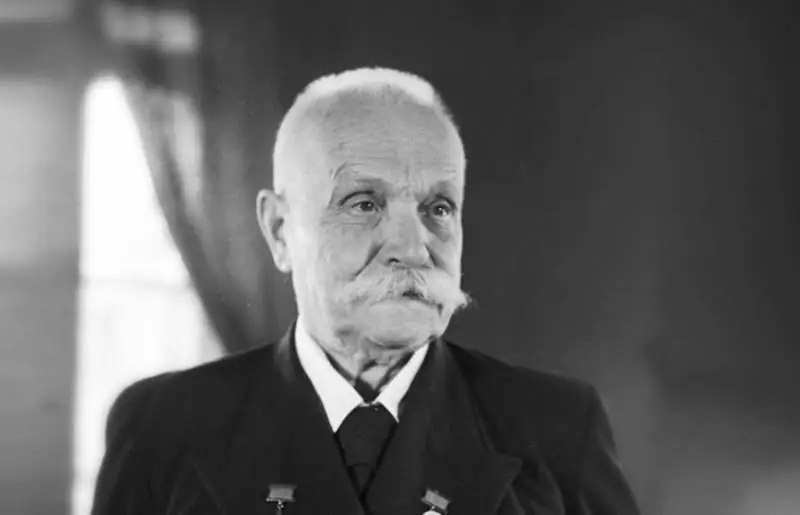
В допълнение към Т-34 заваряването на академик Патон беше използвано в бронирания корпусен корпус № 200 в Челябинск. С негова помощ беше изготвено дъното на корпуса на резервоара KV, което общо възлизаше на около 15 ходови метра от шева на превозно средство. Важно е, че автоматизацията на заваряването на бронята направи възможно привличането на нискоквалифицирани работници в производството - майстори заварчици през цялата война имаше хроничен недостиг. От юли 1942 г. в Нижни Тагил работи уникален танков транспортьор, на който работиха 19 автоматични заваръчни устройства с потопена дъга. Оценете мащаба на иновацията-това освободи 280 висококачествени заварчици за друга работа, замествайки ги с 57 нискоквалифицирани работници. Самият академик Евгений Оскарович Патон в бележка, адресирана до секретаря на отдела за танкова промишленост на Свердловския регионален комитет на Всесъюзната комунистическа партия на болшевиките през март 1942 г., говори за ефективността на въвеждането на автоматично заваряване (цитат от N. Melnikov's книга "Танкова индустрия на СССР по време на Великата отечествена война"):
"Поради високата производителност на високоскоростното автоматично заваряване под слоевете флюс, времето за заваряване на телата ще бъде значително намалено, а потреблението на труд, електричество и електродни тел ще намалее."
Сравнение на времето, прекарано на ръчно и автоматизирано заваряване, може да се намери в архива на изложбения комплекс на ОАО НПК Уралвагонзавод. Според тях на заварчика са необходими малко повече от пет часа, за да заварят например сектор от раменна лента на кула Т-34, а автоматичното заваряване може да направи това само за 40 минути. Долните съединения се заваряват ръчно за три часа, а в автоматичен режим - за един час.
Борба за шева
Не може да се каже, че автоматични заваръчни машини изведнъж се появиха в монтажните заводи на съветската танкова индустрия. Първо, делът на ръчното заваряване все още беше много голям в производството на бронирани изделия, и второ, отначало не всичко беше гладко със самата технология. Не беше възможно да се даде на заварката необходимото ниво на пластичност - след охлаждане тя стана твърда и чуплива. Това, разбира се, имаше най -негативен ефект върху съпротивлението на снарядите на бронята. След анализ на причините се оказа, че всичко е свързано с превишаване на дълбочината на проникване на заварения метал, смесване на металния тел с неблагородния метал и значително легиране на заварения метал. Групи от ЦНИИ-48 под ръководството на И. Ф. Срибни и от Института по заваряване, ръководен от гореспоменатия В. И. Дятлов, предложиха и тестваха следните методи за заваряване на „непоколебими“брони 8С и 2Р. На първо място, това е многоходово заваряване, когато машината свързва частите за заваряване на няколко стъпки. Това гарантира ниско проникване на фугите и образуване на здрав и гъвкав шев. Ясно е, че подобна техника не е най-ефективната във военновременни условия: в края на краищата многопроходното заваряване изисква много време в сравнение с еднопроходния.
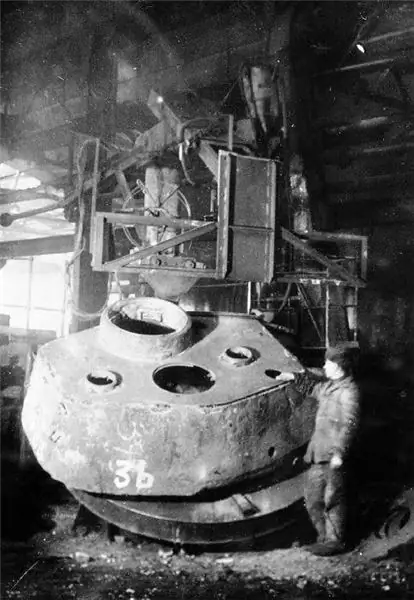
Втората техника от TsNII-48 и Института по заваряване беше полагането на нисковъглеродна стоманена тел в жлеба на шевовете, за да се намали "избледняването" на метала на бронята. В резултат на това шевът след охлаждане стана по -пластичен, телта сериозно намали температурата в канала на шева, а също и удвои производителността на заваръчните машини. Това се оказа най -ефективната техника, която беше допълнително подобрена. Нов метод за заваряване "в два проводника", при който втори (запълващ) проводник, който не е свързан към източника на ток, се подава в заваръчната вана под ъгъл спрямо електродния проводник. Подаването и диаметърът на втория проводник бяха изчислени така, че количеството метал, отложен от него, да е равно на количеството метал от нанесения електрод, т.е. диаметърът на втория проводник трябва да бъде равен на диаметъра на електрода тел и скоростта им на подаване трябва да са еднакви. Въпреки това, поради необходимостта от преоборудване на автоматичните глави от подаване на един проводник до подаване на два проводника, въвеждането на този метод беше отложено и той беше заменен с метода с вмъкване на лента. Независимо от това, още през юни-юли 1942 г. този метод е приложен в завод № 183 при заваряване на партида от долните плочи на носа на корпуса на резервоара с носови греди.
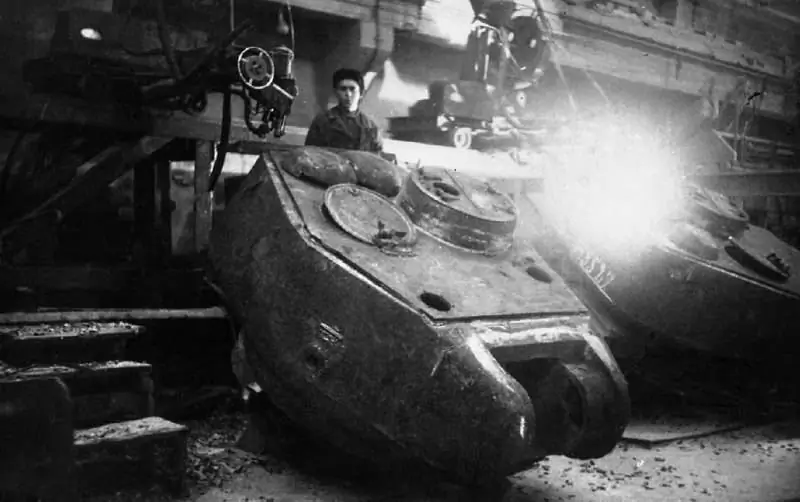
Трудностите с автоматизацията на заваряване на танкови корпуси (кули) също бяха организационни. Струва си да си припомним, че заваръчните машини никога преди не са били сглобявани последователно и всъщност са били продукти от пилотното производство на Института по заваряване. Това обяснява част от бавността в развитието на новите технологии в резервоарната индустрия. И така, до края на 1942 г. танковите фабрики разполагаха само с 30 до 35 заваръчни машини, което, разбира се, не беше достатъчно. Следователно народният комисар И. М. Залцман със заповед No 200 от 28 март 1943 г. разпорежда в завод № 183 допълнително да инсталира 7 автозаваръчни агрегата до средата на май в Уралския завод за тежко машиностроене до 1 юни 8 автомати и до 15 юни 5 единици поискаха да бъдат доставени в завода в Челябинск. No 200. Тази стъпка беше една от многото, които позволиха на местната танкова индустрия да постигне планираните производствени цели за така необходимите гусенични бронирани машини за фронта.